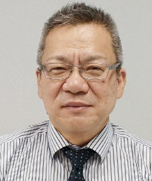
密封品リーク技術部
原 努
7. ファインリーク試験 MIL-STD-883 METHOID1014 SEAL 2.1 A1,A2
(JIS Z 2331付属書D、JIS-C-60068-2-17付属書D)
電子部品の気密性を保証するためにはファインリーク試験が必須である。例えば内容積1cm³の真空封止された試験体に1E-09Pa・m³/secの小さなリークがあった場合、1日程度で100Paも上昇してしまうからである(図6.)。
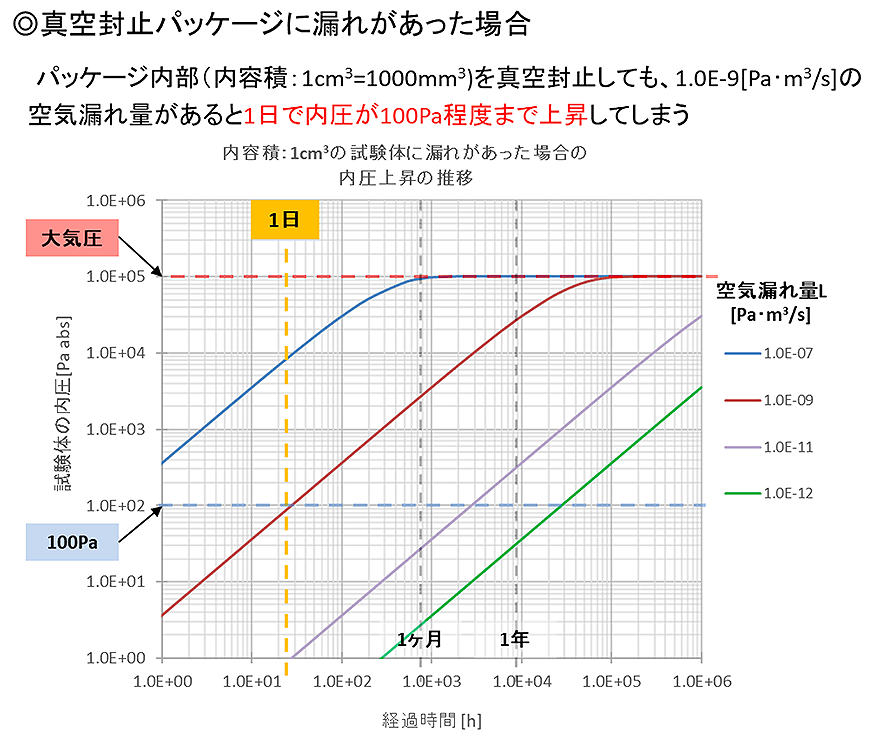
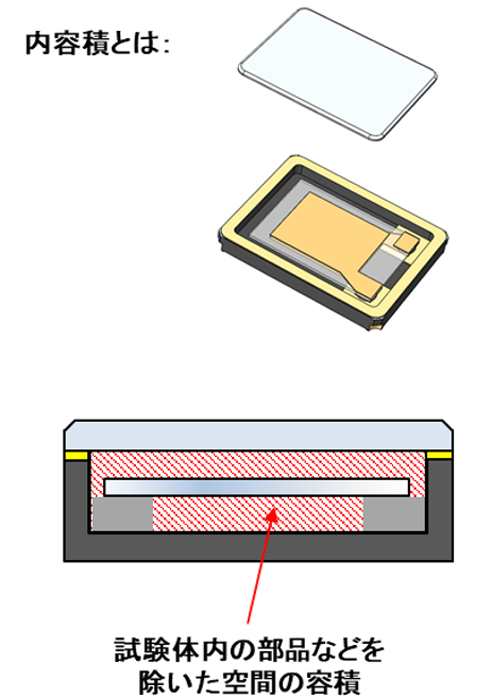
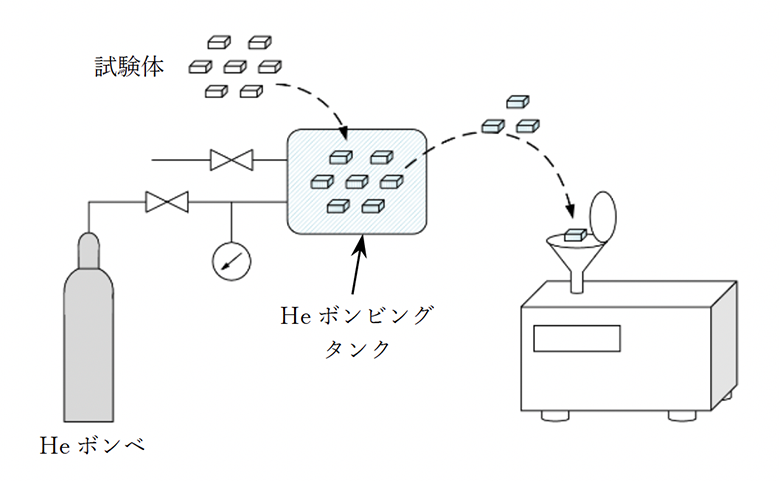
電子部品のような密封製品のファインリーク試験は、サーチガスにヘリウムガスを用いたヘリウム浸漬法(図7.)が主流である。予め試験体をヘリウムガス雰囲気中で浸漬加圧しておき、欠陥のある試験体内部に入ったヘリウムガスを次工程のリークディテクタで検知する方法である。
ラインで採用されているリークディテクタはターボ分子ポンプ一体型が多く、ターボ分子ポンプによる高い排気性能と、ヘリウムや水素など軽いガス分子の逆拡散現象を併用して、ヘリウム検知管に届く邪魔ガスや汚染物質を減らして実用感度の向上と長寿命化が図られている。
ヘリウム浸漬法では、等価標準リーク率Lを有する試験体の測定ヘリウムリーク量R1は、Howell-Mann式と呼ばれる式(1)で与えられると考えられる。第1項が等価標準リーク率に対するヘリウム流量を、第2項が浸漬時間で入るヘリウム量を、第3項が放置時間後に残存するヘリウム量を計算している。

R1 = 不合格にするヘリウムの最大許容リーク測定値(ヘリウムリーク量)
L = 最大許容等価標準リーク率(標準空気流量)
PE = ボンビング圧力 (絶対圧)
PO = 大気圧(絶対圧)
MA = 空気の分子量
M = トレーサガス(ヘリウム)の分子量
t1 = ヘリウムボンビング時間
t2 = ボンビング後、リーク試験までの滞留時間(放置時間)
V = 試験体内の空間容積(内容積)
ヘリウム浸漬後は、測定までの間は試験体内部に浸漬したヘリウムガスは欠陥を通じて放出されるため、ボンビングタンクから試験体を取り出した後は、試験体表面から放出されるリーク以外のヘリウムを減衰させたうえで規定した放置時間以内に測定を完了しなければならない。またヘリウムリークディテクタで測定した値はその時のヘリウムリーク量を示すため必ず等価標準リーク率(空気)への換算が必要となる。
MIL-STD-883 METOD1014 SEALでは試験条件を固定するA1と、式(1)をベースにしてフレキシブルに設定するA2の方法があるが、昨今の電子部品はA1で規定する最小サイズ(0.05cm³=50mm³)より遥かに小さくなっているためA2での検討を推奨する。
最小可検リーク量(R1 )は試験体に大きく依存し、1E-09Pa・m³/s~である。試験品のパッケージにガラス質材料が多いと浸透・離脱ヘリウムが増えて小さなリークが見えなくなる。
本方式でのメリットは、
・定量的な試験が可能で数値管理ができる
・極微小欠陥の検査が可能
デメリットとしては、
・試験用ヘリウムガスが高価で供給リスクもある
・ヘリウム浸漬装置が別途必要
・ヘリウムガス浸漬後の放置時間など試験の管理項目が多い
・内容積の小さい試験体では測定領域が狭まり、グロスリーク試験のリーク領域との重なりが取りづらい
などがあげられる。
8. 不感帯のない試験のために
電子部品の気密試験は、グロスリーク試験とファインリーク試験の2つの試験が必要であり、2つの試験領域に“重なり”がとれて初めて気密性の評価を行ったことになる。すなわち、それぞれの等価標準リーク率(換算)値でみて、ファインリーク試験の上限はグロスリーク試験の下限以上でなければならない。しかし、ヘリウム浸漬法の式1.をベースに計算すると、内容積が0.05mm³の小さな試験体では、実用値(浸漬0.6MPa abs, 1h, 放置時間2分, He判定値1E-09Pa・m³/s)で試験できる等価標準リーク率値は約1E-07Pa・m³/sまでとなり、液没によるグロスリーク試験の下限1E-06Pa・m³/sに達せず、完全なリーク試験にならない。このため下限をより小さくできるグロスリーク試験方法を使う必要がある。
ファインリーク試験としてヘリウム浸漬法を、一方グロスリーク試験として圧力変化法をそれぞれ用いたシミュレーショングラフ(図8.)で説明する。
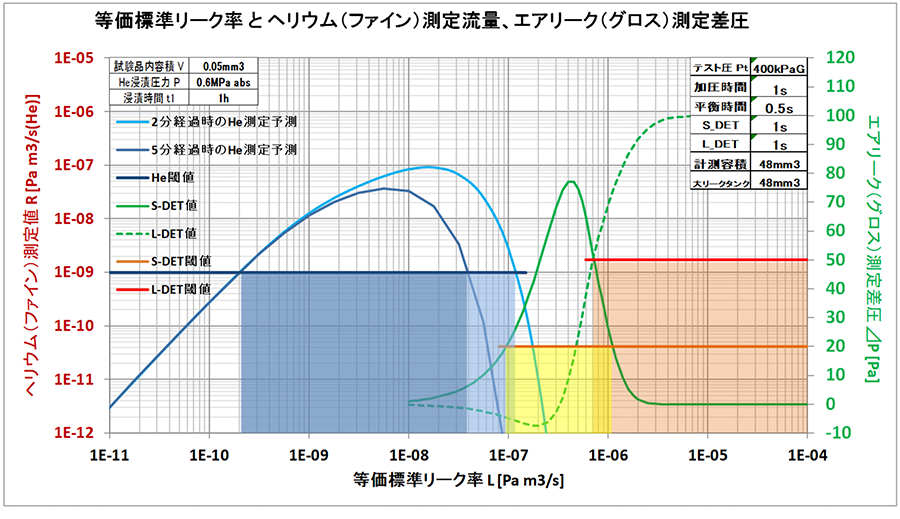
左縦軸は、ファインリークのヘリウム測定値、右縦軸は、グロスリークのエアリーク測定値である。試験体内容積0.05mm³、ヘリウム浸漬0.6MPa abs. 1時間、試験空気圧力400kPaG 1秒としたときを図示している。
グラフ左側には、浸漬終了2分後(水色)と5分後(青色)の測定ヘリウムのシミュレーション値が描かれており、判定するヘリウム測定値(閾値)を1E-09 Pa・m³/sとすれば、浸漬終了2分後では約1E-07 Pa・m³/s、5分後では約4E-08 Pa・m³/sの等価標準リーク率まで試験できることがわかる。
一方、グラフ右側に描かれた差圧測定値のシミュレーション値をみると、グロスリーク試験の下限は8E-08Pa・m³/sで、ファインリーク試験の放置時間2分の検査上限1E-07Pa・m³/sと重なって、不感帯のない試験ができることがわかる。しかし、ファインリーク試験の放置時間が5分では、等価標準リーク率4E-08 Pa・m³/sから8E-08 Pa・m³/s間に不感帯が生じて検査リークが生じてしまうこともわかる。リーク試験では、このような等価標準リーク率による不感帯確認が極めて重要である。
9. おわりに
電子部品の気密試験では、個々の試験の特性やリーク領域を考えて実施されているはずであるが、複数の試験方法で異なるリーク領域を測る場合、とりわけ内容積が1mm³以下の極小さいパッケージの電子デバイス製品やMEMS製品では、上述のような不感帯が発生するリスクが高いため、試験方法・試験の管理方法を十分熟知し数値検討をして実施することが求められている。当社へ電子部品のリークテスト依頼される顧客の中にも良品として判断したものが実はリーク品であったということは少なからず発生している。昨今のような極めて小さな電子部品の試験方法についてはMIL-STD-883でもフレキシブルなA2に沿った試験が必要と考えている。
リーク試験装置の側でも、顧客のリーク試験要求に応えられる高感度化や不感帯の無いリーク試験装置を提供することは重要な課題としていきたい。本稿では触れていないが、MEMS製品のようなごく小さな内容積の製品において、長期の気密性を保証するためのリーク率として、例えば1E-14Pa・m³/sとか1E-15Pa・m³/sが求められることがある。現在では検出限界を超えており、試験方法のブレークスルーだけでなく、こうした欠陥が存在し得るかも含めた孔の最小径などの研究・議論にも期待したい。
引用・参考文献
- 1) JIS Z 2330:2012 非破壊試験-漏れ試験方法及びその選択
- 2) JIS C 60068-2-17:2001 環境試験方法-電気・電子-封止(気密性)試験方法
- 3) JIS Z 2331:2006 ヘリウム漏れ試験方法
- 4) JIS Z 2332:2012 圧力変化による漏れ試験方法
- 5) 例えばMIL-STD-883 METHOD1014 SEAL
- 6) 例えばJIS C 60068-2-17:2001 環境試験方法
- 7) JIS Z 8754:1999 真空技術-質量分析計形 リークディテクタ校正方法
- 8) 国分 清秀他、水晶摩擦真空計と粘性真空計の理論、真空1987 年 30 巻 9 号 p. 706-714
【著者紹介】
原 努(はら つとむ)
株式会社フクダ 密封品リーク技術部
■略歴
2012年 株式会社フクダ入社
電子部品気密検査装置の開発に従事 現在に至る。