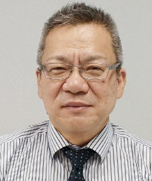
密封品リーク技術部
原 努
1. はじめに
筐体が密封された製品は、内容物を外気から保護できるため、様々な業種の重要な製品・部品で使用されている。そして、その密封容器としての完全性は、製品使途における安全・安心を長期に渡って担保するうえで重要なものとなっている。
本稿では、密封製品のなかでも小型の電子部品を取り上げて、その密封容器の気密試験が実際にどのように行われているかを解説するとともに、試験領域が異なるグロスリークとファインリークの2種の気密試験を行う上での注意点について解説する。
2. 電子部品の気密性とリーク試験
電子部品の気密性が損なわれていると、活性ガスや水蒸気の侵入により電子回路の腐食・劣化が生じたりする。水晶発振子等の電子デバイスでは真空封止した内部に大気が侵入すると周波数特性に変化が生じ、LDやLEDなど不活性ガスで封止されたデバイスでは水蒸気などのガス侵入により光学特性に変化・劣化が生じたりする。
これらの製品では、リークによる不具合の発生を耐用期間に渡って防ぐために、特に非破壊(非侵襲)の試験方法を使い、全数を対象にしたリーク試験がラインで実施される。気密性を評価するリーク試験は試験方法・条件・判定基準は、部品の構造・特性・生産量・内容積等に応じて選定される。
3. 電子部品の封止欠陥
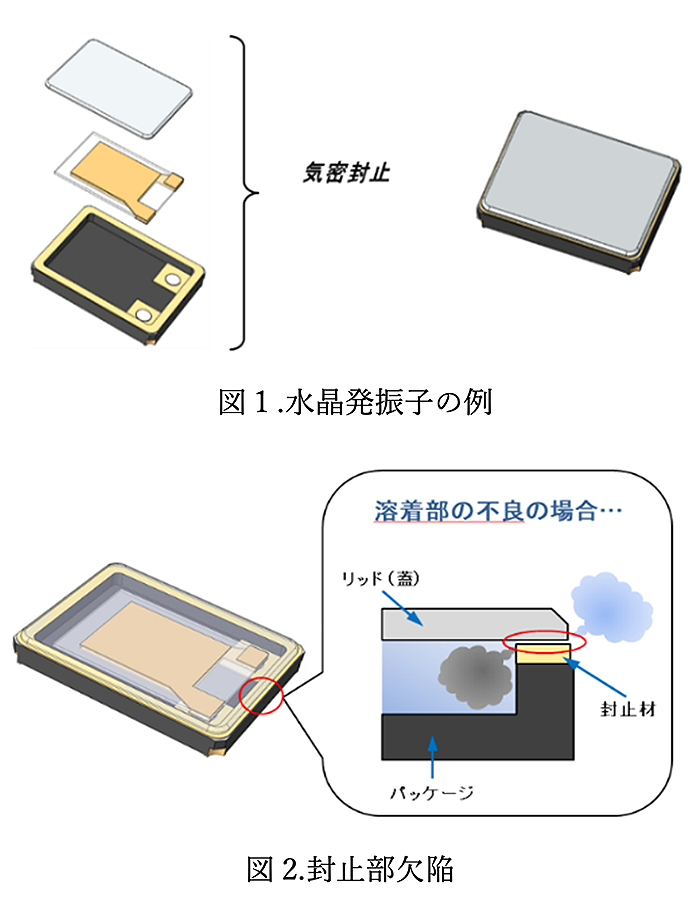
電子部品は有害となるガスから電子回路を保護するために気密封止(ハーメチックシール)された密封構造となっている。表面実装する超小型の水晶発振子を例にとると、振動子回路を搭載するセラミックパッケージと蓋(リッド)と接合のための封止材から構成されており、封止材にはガラスや金属を用いて熱溶着接合されている(図1.)。ガラスや金属はガス透過が少ないので高い気密性は得られるが、製造工程上で発生するリークの発生には十分注意しなければならない。リーク原因の多くはパッケージと封止材部分または蓋(リッド)と封止材間(図2.)の封止不良で発生する。例えば封止材と金属リッドまたはセラミックパッケージとの間で熱膨張率の違いによるクラックの発生、マイクロスクラッチと呼ばれる微細な傷による封止不良、封止部へのダストの噛み込み、封止部への気泡の混入など封止不良には様々な要因がある。このような製造工程内で発生する不良は、全数のリーク検査により排除されている。
4. 電子部品の気密試験方法
電子部品に対する非破壊のリーク試験方法は、例えばJIS Z 23301) の中にまとめられており、密封製品では、液没試験・ヘリウムのボンビング法・圧力変化法密封品チャンバ法の3種となる。個別の規格の詳細は順に JIS C 60068-2-172)、JIS Z 23313) 、JIS Z 23324) に含まれる。また、米国のMIL規格5)は、試験方法と管理基準が詳細に記されており、しばしば標準的に参照される。これに類する規格6)もあるが、本項ではMIL-STD-883 METHOD1014 SEALとJIS Z 2332に依拠しつつ説明する。一部の水晶振動子で有効なCI(Crystal Impedance)8)の原理を使うリーク試験方法など特殊な方法は本稿では割愛する。
1つのリーク試験方法では、欠陥サイズの微小なものから大きなものまで試験できないことから、概略1E-06Pa・m3/s5)を境にして大きな欠陥を検査するグロスリーク試験と微小な欠陥を検査するファインリーク試験の2種を用いる(図3.)。(1E-06=1×10-6以下同様)
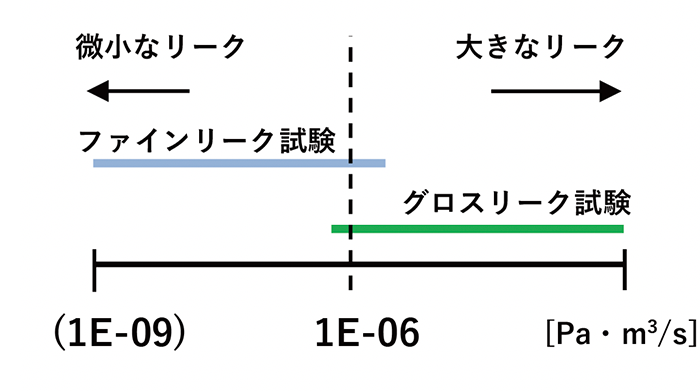
電子部品においても両方を行うが、リーク量の評価は「各試験値を、高圧側1気圧(760Torr)、低圧側2Torr以下における、欠陥を通過する1秒間あたりの25℃乾燥空気量に換算した「等価標準リーク率」を用いて、試験間の領域連続性を確認する必要がある。
*JIS Z 8754 標準空気(換算)リーク量 -25℃より低い露点を持つ空気。入口側100kPa±5%、出口側1kPa未満、温度23℃±7℃
5. グロスリーク試験 MIL-STD-883 METHOD1014 SEAL 2.3.3 C1
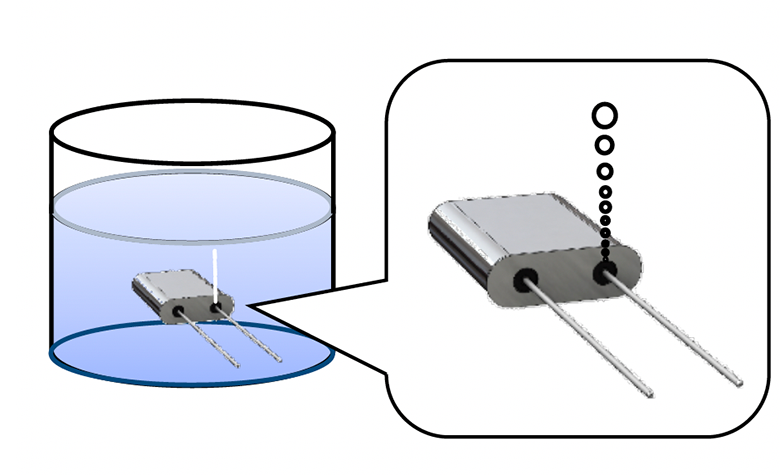
液没試験は、電子部品でもよく実施されるグロスリーク試験である。中でもフッ素系不活性液体を利用した液没試験方法がよく用いられる。
フッ素系不活性液体としては、パーフルオロカーボン(PFC:3Ⅿ社フロリナート)またはパーフルオロポリエーテル(PFPE:ゾルベイ社ガルデン)が使用される。
試験方法は、真空引きした電子部品を低沸点(56℃)のフッ素系不活性液体中に浸漬加圧したのち、125℃の高沸点(165℃)のフッ素系不活性液に浸漬し、出てくる気泡を調べる方法(図4.)である。表面張力及び粘度が低いため水没試験に比較してより小さい孔のリーク検知が可能になり、検出感度はおよそ1E-06Pa・m³/sに達する。
より簡単な、低沸点液体に浸漬加圧しないまま165℃のフッ素系不活性液体に入れて気泡を調べる方法では、感度はおよそ1E-04Pa・m³/sになる。
フッ素系不活性液体を利用した液没試験方法のメリットをあげると、
・比較的簡便な方法であるが高感度1E-06Pa・m³/s
・気泡発生部位から不良個所の特定が可能
・フッ素系不活性液体は化学的に安定・不活性で製品を傷めない
などがあり、一方デメリットとしては、
・定性的な試験であり定量的な管理ができない
・自動化が難しく作業者の技量・状態に影響を受け、ヒューマンエラーの可能性
・フッ素系不活性液体は高価で揮発物は温室効果ガス
留意点として、
・電子部品の耐熱温度、試験液の管理、ファイン試験を先に実施
などがあげられる。
6. グロスリーク試験 JIS Z 2332(附属書D圧力変化法 密封品チャンバ法+F 差圧法)
圧力変化法によるグロスリーク試験は、分解能1Pa程度の差圧計で微小な圧力変化を捉えてリークを検査する方法である。試験気体として空気を使え、液没試験に比べ自動化が出来ることや、差圧法の併用で試験感度を向上できることから、近年、ライン採用が増えてきた方法である。
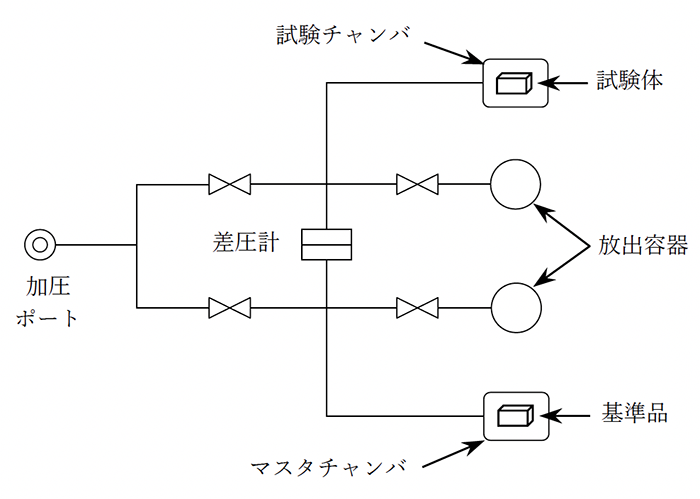
密封品チャンバ法に差圧法を併用した圧力変化法の測定原理図を図5.に示す。マスタチャンバに基準品(リークの無い良品)を入れ、差圧計を挟んで対称となる試験チャンバに検査する製品(試験体)を投入して空気圧を印加する。試験圧力の印加後に閉回路とし、欠陥のある試験体のパッケージ内部へ空気が侵入するときに生じる圧力降下をマスタチャンバ側圧力と比較してリークを検知する。この時、パッケージの蓋(リッド)が外れているような欠陥では試験圧力の印加時に圧力平衡して差圧が発生しないが、次に「放出容器」側の弁を開けると、(大リーク品の内容積分の)空気量が多い試験チャンバ側はマスタチャンバ側より圧力が高くなるため、大きな欠陥品の検知も可能になっている。
この圧力変化法は、精密な検査装置を必要とするが、高い生産性があることから、水晶発振子やLED部品、電解コンデンサ等のグロスリーク試験での利用が広がっている。
この方式のメリットは、
・測定回路の内容積を50mm³程度とすることで最小可検リーク量8.5E-08Pa・m³/sが可能
・自動化と多チャンネル化によりスループットを大きくできる。10~個/分・ch
・再現性の高い検査値が得られ数値管理が可能
・試験ガスが空気であるため、試験体の侵襲・環境影響が無くランニングコストも安い
などであり、一方デメリットとしては
・圧力変化でリークをみているため欠陥箇所の特定ができない
・測定感度を向上するために試験体形状に合わせたカプセル(試験容器)が必要
・マスタ(基準品)が試験チャンネル分必要、などがあげられる。
次回に続く-
引用・参考文献
- 1) JIS Z 2330:2012 非破壊試験-漏れ試験方法及びその選択
- 2) JIS C 60068-2-17:2001 環境試験方法-電気・電子-封止(気密性)試験方法
- 3) JIS Z 2331:2006 ヘリウム漏れ試験方法
- 4) JIS Z 2332:2012 圧力変化による漏れ試験方法
- 5) 例えばMIL-STD-883 METHOD1014 SEAL
- 6) 例えばJIS C 60068-2-17:2001 環境試験方法
- 7) JIS Z 8754:1999 真空技術-質量分析計形 リークディテクタ校正方法
- 8) 国分 清秀他、水晶摩擦真空計と粘性真空計の理論、真空1987 年 30 巻 9 号 p. 706-714
【著者紹介】
原 努(はら つとむ)
株式会社フクダ 密封品リーク技術部
■略歴
2012年 株式会社フクダ入社
電子部品気密検査装置の開発に従事 現在に至る。