4.無機バインダを用いたリチウムイオン二次電池用高機能Si負極の開発
斉藤 誠
4-1. はじめに
リチウムイオン二次電池の用途拡大、とりわけEV(電気自動車)分野での採用に伴い、高容量化、高出力化などの性能向上の要求はこれまで以上に加速している。シリコン(Si)はグラファイトの10倍程度の電気容量を有し、かつ、地表に含まれる金属元素として最多であり資源としても豊富なことから、次世代リチウムイオン二次電池の負極活物質として有望である4-1)。一方、充放電に伴う体積変化が大きく、そのため、サイクル特性が劣る問題があった。Si負極の劣化は複数のメカニズムによって進行するが、極初期の劣化要因として、電極基材からの活物質層の剥離や活物質層内での導電ネットワークの破壊4-2)が挙げられる。この解決策として、ポリイミド4-3)などの高強度樹脂バインダをはじめ、バインダの改良によるアプローチが検討されてきている。本稿では、大阪産業技術研究所とATTACCATO合同会社(大阪府和泉市)が共同研究のもと開発した、無機バインダによるSi負極のサイクル特性改善やその作用機序について紹介する。
4-2.ケイ酸塩系無機バインダを利用したSi負極の作製
4-2-1.電極コーティング剤としての利用
ケイ酸塩系無機バインダは19世紀中ごろには「水ガラス」として防火剤や接着剤、木材や石材、コンクリートなどの強度を高めるためのコーティング剤に利用されてきた材料である4-4)。シロキサン結合(Si-O-Si)を骨格とした強固な結合力に加え、有機樹脂系バインダと比べて圧倒的な耐熱性や耐酸化性を特長とする。一方、有機樹脂系バインダと比べて比重が大きく、バインダとして単用した場合、重量効率の点で問題がある。そこで、ケイ酸塩系無機バインダを活物質層にコーティングし、活物質粒子間に強固な骨格構造を形成する電極構造を考案した。
無機バインダコートSi負極は、従来のグラファイト系負極と同様の手法でSi電極を作製したのち、無機バインダ水溶液をスプレー、乾燥・熱処理の工程を経て作製できる。本手法で必要とする熱処理温度は140~160 ℃であり現行のグラファイト系負極製造設備を流用できる。これは、硬化処理に200~300 ℃の真空熱処理を要するポリイミド系バインダと比較して設備投資・開発期間短縮の点で大きな利点となる。
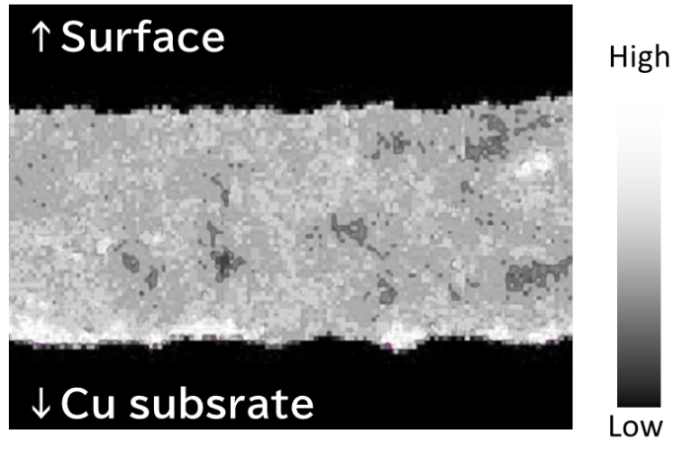
EPMAを用いて断面方向への元素分布を確認したところ、無機バインダに由来するNaは主に活物質粒子の隙間を埋めるように存在しており、また、電極表面から内部まで均一に分布していることが確認された(図4-1)。すなわち、活物質層の空隙部分を強固な無機バインダが骨格形成材として充填している構造が示唆される。また、無機バインダをコートすることで、活物質層の機械強度および密着力は大きく増加した。
無機バインダコートの有無によるサイクル特性の違いを図4-2に示す。無機バインダをコーティングしていない場合、初回サイクルでわずかに放電するものの、サイクル特性は極めて乏しかった。無機バインダのコーティングによりサイクル特性は大きく改善した。
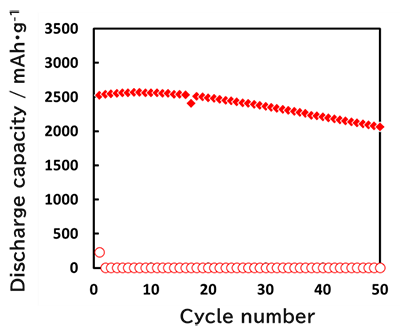
[◆:コートあり、○:コートなし]
初回サイクル前後のSi負極の断面を図4-3に示す。無機バインダコートの有無にかかわらず、充放電前の電極では活物質層と電極基材は良好に密着しているものの、無機バインダをコーティングしていない場合、初回の充放電サイクル後に活物質層が電極基材から剥離する。一方、無機バインダをコーティングした電極では活物質層の剥離は見られなかった。
これらの挙動の違いは、無機バインダの強固な結着性によるものと考えられる。PVdFや SBRなど従来、用いられてきたバインダは結着力の弱いため充電時のSi粒子の体積膨張に耐えることができず、活物質層が基材から剥離する。ここに、無機バインダをコーティングし、活物質間を強固な無機バインダ成分で充填することで結着力を高め、その結果、活物質層の剥離を抑制できたと理解している。
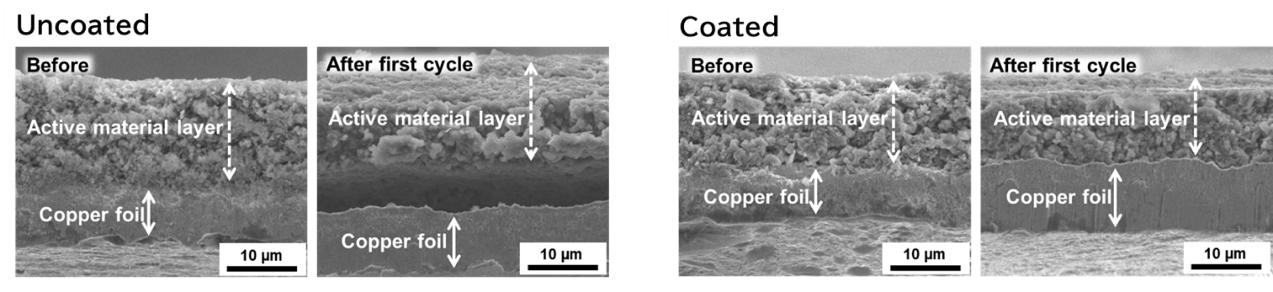
4-2-2.コーティング量・組成の最適化
無機バインダのコーティング量には最適値が存在し、活物質のSiに対しおおむね6~50%程度の重量比の場合に電気容量・サイクル特性とも良好な結果が得られた。一方、過剰の無機バインダは放電容量を低下させた(図4-4)4-5)。
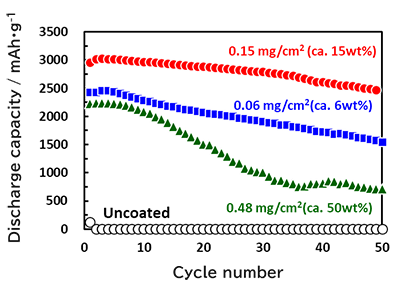
この理由は、Si負極にコーティングした無機バインダは活物質層に浸透し粒子間の骨格形成剤として働くが、余剰の無機バインダ成分は電解液と活物質の接触を阻害したり、リチウムイオンの拡散を妨げたりするためと考えられる。また、無機バインダコート後の乾燥速度が不適正だと、電極内部まで十分浸透する前に表層付近で乾燥し、充分に骨格が形成されないためサイクル特性に劣ることも合わせて確認している。これら、無機バインダのコート量や乾燥の良否など、量産時の生産管理には迅速に深さ方向への元素分布が評価できるGD-OESが有用である4-6)。
4-3.無機バインダの作用機序に関する考察
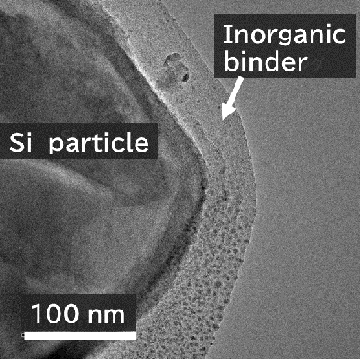
無機バインダによるサイクル特性向上のメカニズムを調べるために、Si負極のSTEM観察を行った(図4-5)4-7)。Si粒子の周りに厚み20~50 nm程度の無機バインダによる皮膜が形成されており、その界面は不明瞭なアモルファス状であった。すなわち、無機バインダのシラノール基(Si-OH)とSi粒子表面の水酸基(-OH)とが脱水縮合することで強固なシロキサン結合(Si-O-Si)を形成している構造が推察される。また、無機バインダはSi粒子だけでなく、電極基材(Cu箔)表面の自然酸化被膜に由来する水酸基とも脱水縮合することで、Si粒子と電極基材とを強固に接着し、充電時の体積膨張による剥離を抑制していると考えられる。
4-4.おわりに
本技術を用いてラミネート型電池(5Ah級)を試作したところ、その重量エネルギー密度は289 Wh/kgと、現行のEV(電気自動車)に搭載されている電池パック(200〜250 Wh/kg)と比較しても高い重量エネルギー密度を達成した。また、0℃付近での低温でも安定に動作することに加え、釘刺時の発火・爆発の危険性も抑制できることが確認されている。これらの諸特性が、生態調査(バイオロギング)用の電源として着目され、亜南極圏での生態調査等に採用されている4-8)。
謝 辞
本研究の一部は 「和泉市ものづくり技術商品開発事業」 「大阪府ものづくりイノベーション支援プロジェクト」 の助成を受けて行われた。関係各位に深く感謝する。
参考文献
4-1) T. Sakai, Electrochemistry, 71(8), 722 (2003).
4-2) D. Reyter, S. Rousselot, D. Mazouzi, M. Gauthier, P. Moreau, B. Lestriez, D. Guyomardéa and L. Roue, J. Power Sources, 239, 308 (2013).
4-3) M. Morishita, A. Yamano, T. Kitaoka, H. Sakai, T. Ojima and T. Sakai, J. Electrochem. Soc., 161, A955 (2014).
4-4) J. Nepomuk Fuchs, Polytechnisches Journal, 17, CIV, 465 (1825).
4-5) 岩成大地、吉田一馬、田中一誠、坂本太地、山下直人、池内勇太、佐藤淳、綿田正治、向井孝志、第58回電池討論会, 1B16 (2017).
4-6) 斉藤誠、西村崇、向井孝志、坂本太地、山下直人、池内勇太、第59回電池討論会、2A05 (2018).
4-7) 髙橋牧子、木下智博、田名網潔、青柳真太郎、向井孝志、池内勇太、坂本太地、山下直人、Honda R&D Technical Review, 33 (1), 78 (2021).
4-8) https://www.youtube.com/channel/UCcn6Oh5y6eu-G1Qsl1xJ_Bw, 参照日:2022-01-11.
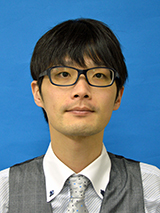
【著者紹介】
斉藤 誠(さいとう まこと)
2009年3月大阪大学大学院工学研究科応用化学専攻博士後期課程程了。
産業技術総合研究所ポスドク、大阪大学技術職員を経て、2013年4月より、地方独立行政法人大阪府立産業技術総合技術研究所(現大阪産業技術研究所)にて、リチウムイオン電池、キャパシタなど蓄電材料の開発、材料評価、表面分析などに従事。
現在、同所、金属表面処理研究部、表面化学研究室、主任研究員。博士(工学)。
5.銅合金材料の金属3Dプリンティング技術の開発
中本 貴之
5-1. はじめに
金属3Dプリンティング(積層造形法)は、3次元CADデータに基づいて一層ずつ積み上げながら加工する付加製造法(AM; Additive Manufacturing)である。その特長は、従来の金属加工(機械加工、塑性加工、鋳造など)では製造できない複雑形状を比較的短時間で造形できる点である。工業分野では内部に任意の冷却流路を有する射出成形金型やジェットエンジンの燃料噴射ノズルなど、医療分野ではテーラーメイドの人工股関節や歯科補綴物など、金属3Dプリンティングの特長を活用したものづくりは盛んになってきている。
金属粉末を直接溶融・凝固させる3Dプリンティングの方式には、粉末床溶融結合法[Powder Bed Fusion (PBF)]と指向性エネルギー堆積法[Directed Energy Deposition (DED)]の2種類がある。PBFは図5-1に示すように、金属粉末をブレードと呼ぶワイパーで平面上に薄く敷き詰め、造形したい部分にのみレーザあるいは電子ビームを照射して粉末を溶融・凝固させる工程を繰り返しながら所望の形状を造形する。一方、DEDは図5-2に示すように、ノズルから金属粉末の投入とレーザの照射を同時に行いながら基材とともに粉末を溶融・凝固させ、ノズルを移動させていくことで肉盛り溶接しながら所望の形状を造形する。両者を比較すると、より高精度に内部構造を造形できる手法はPBFであり、PBFタイプの金属3Dプリンタは世界中で広く普及している。
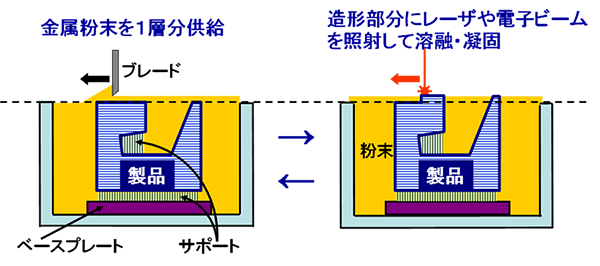
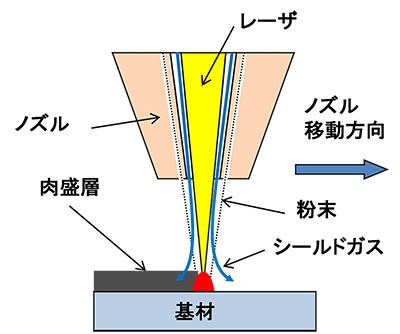
PBFで一般的に使用される金属材料は、鋼、チタン合金、アルミニウム合金、ニッケル基超合金など多岐にわたるが、銅はレーザを反射しやすく、かつ熱伝導率が高いため、造形物の高密度化が難しいと言われてきた。そのため、高い電気伝導性や熱伝導性が要求される機能部品を金属3Dプリンティングで実現するためには、新たな銅系材料とその造形技術を開発する必要があった。本稿では、大阪産業技術研究所と株式会社ダイヘンが共同研究のもと開発した銅合金粉末およびそのPBF造形技術と、株式会社ダイヘンが実用化したアーク溶接用高電流水冷トーチについて紹介する。
5-2.銅合金粉末およびそのPBF造形技術の開発5-1)
純銅粉末を用いて、ドイツ製EOSINT M280金属3Dプリンタにより作製した造形物の断面写真の一例を図5-3に示す。黒色の領域は空隙に相当する。純銅粉末では、造形時のレーザ照射条件(出力、走査速度、走査間隔、および積層厚さ)を変化させても、高密度な造形物が得られなかった。そこで我々の研究グループは、種々の銅合金材料を用いて造形実験を繰り返す中で、銅にクロムを少量添加した銅合金(Cu-Cr)粉末を用いることにより、ほとんど空隙が認められない高密度な造形物を得ることに成功した(図5-4)。高密度化の要因の一つとして、今回用いたレーザと同じ波長の光の反射率は、純銅粉末に比べCu-Cr粉末のほうが20%程度低下しており、溶融しやすくなったためと考えられる。しかし、添加元素量が増えると銅合金の導電率は低下することが知られており、実際にCu-Cr造形物の導電率は造形ままの状態で20%IACS程度とかなり低い値であった。
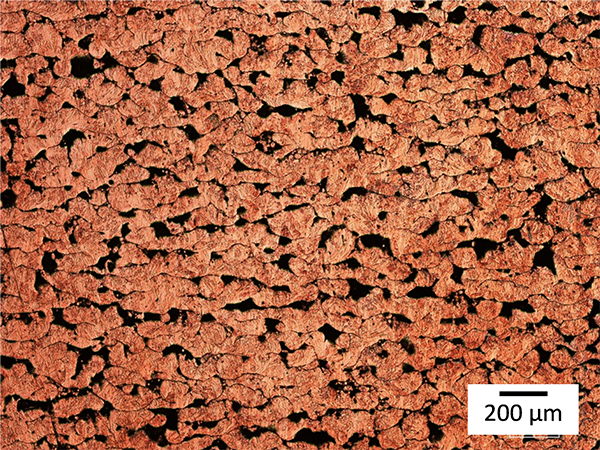
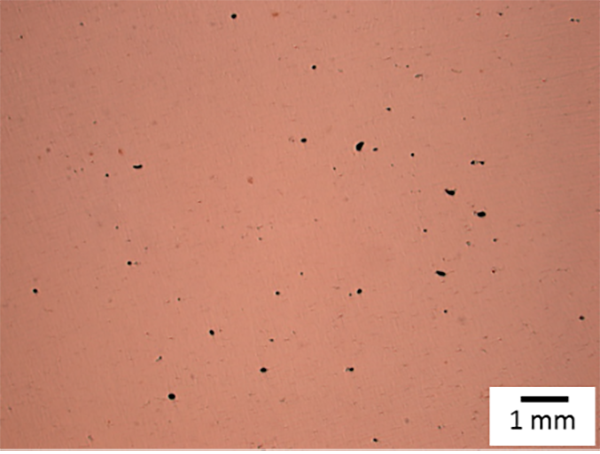
そこで熱処理(各温度1時間)による導電率の改善を試みた。図5-5に示すように、400 ℃以上の熱処理により、導電率は大幅に上昇している。これは、レーザ照射による急冷凝固に起因して、造形ままの状態でCuマトリックス中にCrが過飽和に固溶しており、それが熱処理により時効析出して固溶量が減少したためと考えられる。
図5-5には機械的性質として引張強さの結果も示してあり、引張強さは400~600 ℃の範囲の熱処理により上昇し、450 ℃において最高値を示す。ここでは熱処理前に溶体化処理を施していない。Cu-Cr合金の造形物では、上述のようにレーザ照射による急冷凝固の効果で、溶体化処理を施さなくてもCrがCuマトリックス中に過飽和に固溶し、時効処理のみで硬化したと考えられる。 以上のように、用途に応じて造形物の特性を任意に変更することができ、導電率を重視する場合は導電率を純銅の90%程度まで、機械的性質を重視する場合は引張強さを純銅の3倍程度まで高めた造形物の作製が可能になることを見出した。本銅合金粉末およびその造形技術は、2016年10月にプレスリリースし5-2)、各方面から注目を集めている。
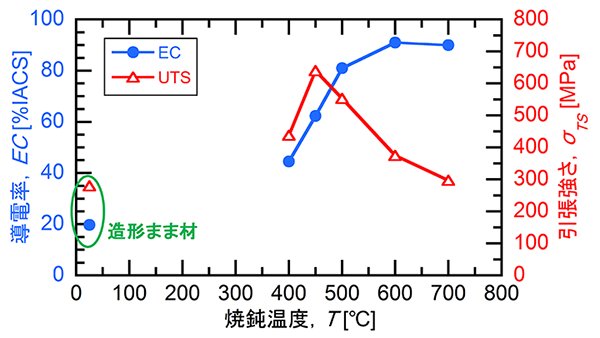
なお、本銅合金粉末とその造形物を対象とした特許は、国内外で複数取得済である。現在、本銅合金粉末は三井金属鉱業株式会社から製造、販売されており5-3)、一般の装置ユーザーにも開放している。
5-3.溶接トーチの実用化5-4)
株式会社ダイヘンでは、本造形技術を応用して、高能率アーク溶接システム「D-Arc」用の高電流水冷トーチを開発した(図5-6)。金属3Dプリンティングの特長である複雑形状を活用し、最適な水冷経路を構築することで、従来なし得なかった高冷却機能と小型軽量化を実現している。
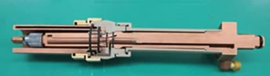
5-4.おわりに
大阪産業技術研究所の和泉センター内に令和3年4月に開設された「3D造形技術イノベーションセンター」5-5)は、PBFタイプ3台、DEDタイプ1台の計4台の金属3Dプリンタを所有している。また、造形物の高機能化につながるトポロジー最適化設計や、造形不良を回避できる熱変形シミュレーションといった、実際の造形前に設計・解析できるソフトウェアも取り揃えている。本センターは、これらの装置およびソフトウェアを駆使して、材料・造形技術、設計・解析技術、特性評価技術など各要素技術の研究開発を一貫して支援できる金属3Dプリンティングの拠点として活動中である。企業、大学、研究機関など利用者の皆さまには、製品開発、試作のスピードアップ、製品の高度化など、専門研究員からの技術支援やアドバイスのもと、研究開発を推進していただきたく、まずはお気軽にご相談ください。
参考文献
5-1) S. Uchida, T. Kimura, T. Nakamoto, T. Ozaki, T. Miki, M. Takemura, Y. Oka and R. Tsubota, Mater. Des., 175, 107815 (2019).
5-2) 株式会社ダイヘンWebページ,金属3Dプリンタによる銅合金3D積層造形技術を確立,https://www.daihen.co.jp/newinfo_2016/news_161026.html, 参照日:2022-01-11.
5-3) 三井金属鉱業株式会社Webページ,3D積層造形用銅合金粉,https://www.mitsui-kinzoku.co.jp/project/kinousei-funtai/custom.html, 参照日:2022-01-11.
5-4) 株式会社ダイヘンWebページ,銅合金3D積層造形技術,https://www.daihen.co.jp/tech/3dprinter/, 参照日:2022-01-11.
5-5) 地方独立行政法人大阪産業技術研究所Webページ,「3D造形技術イノベーションセンター」の開設,https://orist.jp/kouhou/press_release/2021042702.html, 参照日:2022-01-11.
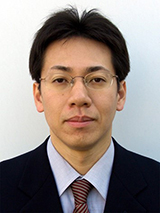
【著者紹介】
中本 貴之(なかもと たかゆき)
1997年3月京都大学大学院工学研究科修士課程修了。
1997年4月より松下電器産業(現パナソニック)株式会社勤務を経て、2004年4月より、大阪府立産業技術総合研究所(現大阪産業技術研究所)にて金属粉末積層造形法における造形物の高性能化に関する研究開発に従事。
2010年9月京都大学大学院工学研究科博士後期課程修了。
現在、同所、加工成形研究部、特殊加工研究室長(主幹研究員)。博士(工学)。
6.結 言
4つの事例を通じて、その背後にあるオープンイノベーションを成功させるカギ、オープンイノベーションの重要性を感じ取っていただければ幸いです。とくに、これらの事例で共通して言えることは、オープンイノベーションを成功させるために、ものづくり企業と大阪技術研の担当者間で、組織内外での調整を含め、確固としたネットワークを構築してきたことが挙げられます。
大阪技術研は、単に製品開発のイノベーションに資する技術を提供するだけでなく、マーケティング、市場調査などの領域でもオープンイノベーションを確立できるよう、官公庁や金融機関を含む支援機関とのネットワークを強固なものにし続けています。加えて、変化の激しい現代社会において、ものづくり企業のニーズに応え続けていくためには、常に新しいアイデアや技術を大阪技術研外から取り入れることが極めて重要と考え、戦略的に、アイデアや技術の取り入れを実施し、大阪技術研のあるべき姿を追い求めています。
とくに、今後、人材などのリソースの機動性が一層高まり、国内のみならず国際的なオープンイノベーションを多くの企業が実施することになってきます6-1)。そのため、大阪技術研では、安全保障輸出管理制度6-2)に留意しつつ、オープンイノベーションにおけるリスクや課題の整理とともに、新型コロナウイルスによる生活の変化にも十分に対応できる体制(オープンイノベーションプラットフォーム)づくりを目指しています。
参考文献
6-1) 例えば、https://www.mext.go.jp/b_menu/shingi/gijyutu/gijyutu11/siryo/attach/1333196.htm, 参照日:2022-01-11.
6-2) 例えば、https://www.meti.go.jp/policy/anpo/gaiyou.html, 参照日:2022-01-11.
7.謝 辞
大阪技術研、和泉センターが実施してきたオープンイノベーションを通じた研究開発事例について、紹介できる貴重な機会をいただき、深く感謝申し上げます。紹介しました事例を参考に、大阪技術研と協業、共創することで、新たな市場を切り開き、新しい商品の創出に繋がることを少しでもご理解いただければ、幸いです。
なお、本レポートでは、和泉センターのオープンイノベーションの事例を紹介しましたが、森之宮センターでも積極的にオープンイノベーションを推進しております。引き続き、両センターともに、みなさま方から多くの利用があることを願っています。

【著者紹介】
櫻井 芳昭(さくらい よしあき)
1989年4月より、大阪府立産業技術総合研究所(現大阪産業技術研究所)にて、ディスプレイ、光学素子、電池の開発に従事。
2002年3月大阪大学大学院工学研究科博士後期課程修了。
現在、同所和泉センター研究管理監兼経営企画本部マネージャ(総括研究員)。博士(工学)。